Electrical and fluid engineering from a single source
The Schimpke GmbH & Co. KG optimizes the synergy effect of combining fluid and electrical engineering at the level of design.
The connection of electrical and fluid engineering is especially meaningful for the design of machine tool cooling systems, because the cooling media is fluid and the systems are steered with electrical or electronic control elements. The Schimpke GmbH & Co. KG optimizes the synergy effect of combining fluid and electrical engineering at the level of design: The designers are always responsible for both trades and use the interdisciplinary EPLAN Platform for that purpose. Modern machine tools work with spindle rpm of up to 70 000 min -1 and a correspondingly high performance -- and that on more and more limited space. The unavoidable result is heat buildup, which then needs to be dissipated. The demand for this thermal management continues to grow, as power and compactness are increased. Because extreme heat accumulation does not only lead to early wear of the tooling and unplanned downtime for the machine; the heat expansion also affects the dimensional stability and tolerances of the pieces that are processed on the machines. This is why the know-how of the Helmut Schimpke Industriekühlanlagen GmbH & Co. KG in Haan, at the Rhein river is in demand worldwide. Schimpke has specialized in the development and production of chillers for machine tools. The company was founded in 1955. It has concentrated on custom developed systems for large machines that perform high precision processes, like for instance on car chassis parts or components for aircraft. Many well known manufacturers of machine tools utilize their systems. Each system is designed individually
The project requirements have to be agreed on with the customer at the beginning of each venture. Michael Stader, Technical director of the company: "We determine the cooling capacity based on the data provided to us. Other requirements to be cleared up are the cooling unit integration into the machine, the space available, and the type of steering." Schimpke designs a project specific cooling unit with this data, which then provides consistent temperatures for work pieces and tools regardless of the ambient conditions. In many cases even the drives are included into the cooling system requirements. Exact control of the temperature levels is achieved with electric or - depending on the customers' request - electronic control loops, which include, among other things, pumps, valves, pressure switches and sensors. "One for all"
Schimpke GmbH has set up an anomaly in the otherwise very team focused world of machine design. Each one of the three design engineers is responsible - and that across all trades involved - for one complete project each. Michael Stader: "This way a system is built by 'a single source' where the process engineering and the electronics are aligned to each other perfectly. "Even the cooling system layout with its customized software is part of the responsibilities assigned to the designers. A discipline spanning CAD infra structure matches the likewise design approach, and Schimpke has coupled that with the EPLAN Platform for three years now. Michael Stader: "We have been working with EPLAN for three years now, have always kept the system current, and added the fluidPLAN to our setup rather early on; the close connection of electrical and fluid engineering meant a huge work reduction for us and our design departments. We were therefore immediately convinced, when EPLAN introduced the new platform about three years ago, with EPLAN Electric P8 and EPLAN Fluid using the same data base. Stefan Greiser, technical order processing: We look at "Electrical and fluid engineering as two sides of the same design. Changes made on one level do have a direct effect on the other. EPLAN Platform automatically transfers the results over to the other related levels. This has helped to prevent errors - which in turn speeds up the design tremendously." Storing design modules as macros
Designers usually work along the variant principle, in order to save time and to be able to use tried and proven designs. They use modules for that purpose that have been stored as macros. Stefan Greiser: "We already used macros in EPLAN 5.70. Since we use EPLAN Electric P8, we have made more intensive use of macros, primarily because using them has become so much more diverse and easier." Modules like power infeeds for example, motor junctions, power packs and speed controls can all be stored as macros. All the designer has to do is call up the macros, define the respective power and adapt the device tags, done. The database contains these modules sorted into output categories. Stefan Greiser: "Keeping this database current does require a certain amount of manpower, but it is definitely worth the effort: This will save time later during each new project." Exactly that was the reason why Stefan Greiser just recently migrated and stored all Profibus modules used for designing into the database. Fluid engineering design with EPLAN Fluid is just as simple. For instance, the system generates all connections automatically and attaches logical properties to each component used. Technical data, on the other hand, like diameter, operating pressure or flow rate are stored in the Parts management. This provides the design department with a more systematic foundation and the designer does not have to look up the data in the manufacturer's documentation. The largest benefit for Schimpke is the improved macro engineering of EPLAN Fluid, which is able to store entire circuit sections on the fluid technology level as well. This feature greatly simplifies variant construction. Never leave anything to chance
After a thorough check on a test bench at their facility, Schimpke delivers customized cooling systems ready to plug in. All operating states are simulated during this process and the test results documented. The company often delivers the EPLAN files along with the plant system. Michael Stader: "Many of our customers really appreciate that. We enter the plant location and they are able to download our EPLAN data directly into their documentation. This can be done just as smoothly for Electric P8 data as for EPLAN Fluid." Schimpke is considering EPLAN Cabinet for some time in the future. Michael Stader: "3D design of enclosures would be very helpful, because the collision monitoring function prevents errors." Furthermore, a hose configurator is on the company's wish list, to be used as an add-on module for EPLAN Fluid. Such a configurator is already available, but currently only for hydraulic systems. Stefan Greiser: "We would love to use such a configurator, which is capable of showing the specific line requirements for water emulsions. It would save us the manual creation of a hose list." This list is at this time still established by the field technician and then entered into the EPLAN documentation. With this new configurator Schimpke recognizes the real advantages of decreased mounting times, because the hoses can be pre-cut to size and pressed into shape before installation.
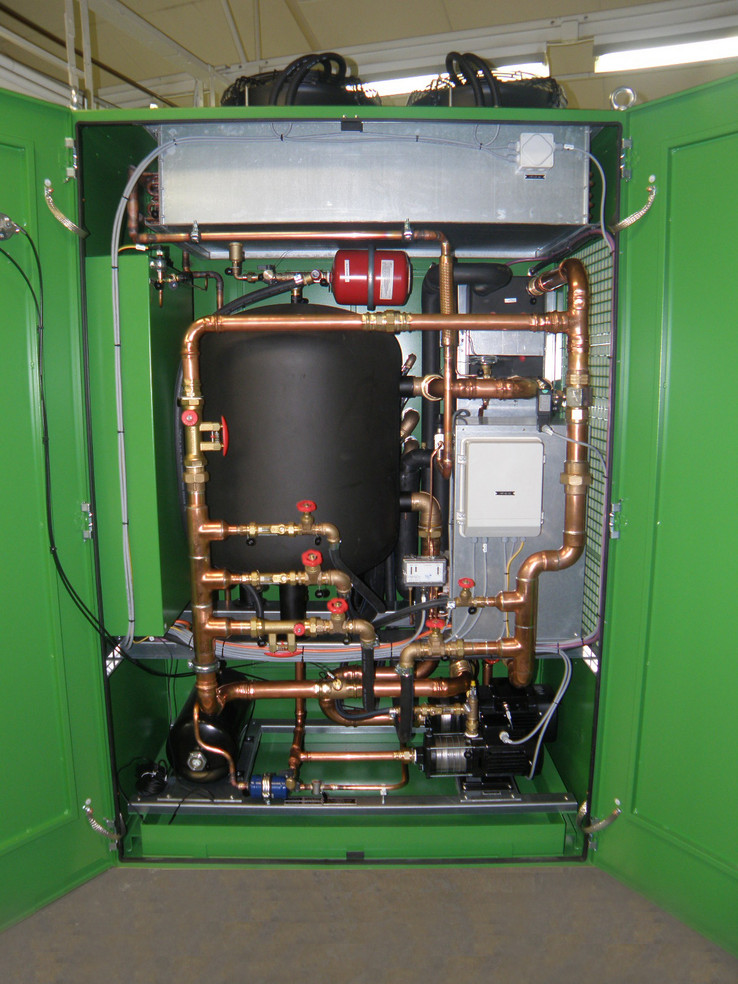
Completely planned, designed and manufactured: Cooling systems by Schimpke ensure even temperature levels for work pieces and tools, and are delivered complete, inclusive electrical and fluid documentation.
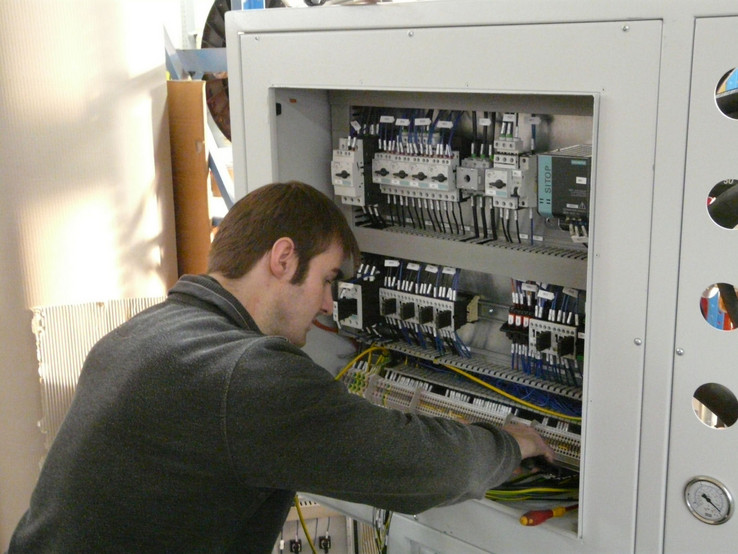
EPLAN Electric P8 facilitates planing of the entire electrical engineering layout, which is the foundation for optimal wiring of an enclosure.
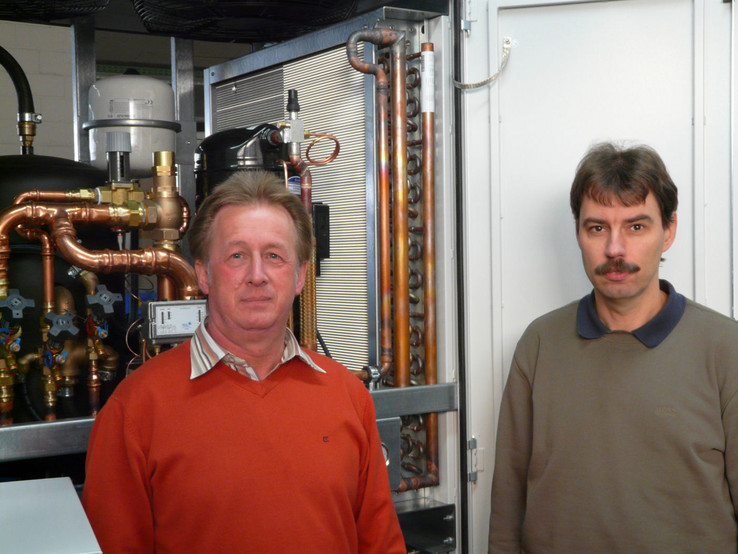
Schimpke holds the designer responsible for the entire project – across all disciplines. Michael Stader, technical director and Stefan Greiser are convinced of the "single source" work approach.